Advertising:
Purchasing Info Record
Get an understanding of Purchasing Info Record (PIR) in SAP ERP system. Also get hints for application, customizing and development.
Overview
In the SAP system, the Purchasing Info Record is a central element in the procurement process. It serves as a master data object that provides detailed information about the relationship between a supplier and a material. Essentially, the PIR is a combination of the vendor and material and contains information relevant to the purchasing process, such as prices, conditions, and delivery terms.
Here’s a breakdown of the key components and importance of a Purchasing Info Record:
Basic Data
- Vendor: The supplier from whom the material will be procured.
- Material: The specific material or product being purchased.
- Purchasing Organization: The organizational unit responsible for procurement activities. This is used to maintain vendor-material data specific to the purchasing organization.
- Plant: The physical location where the material will be delivered (for stock-based procurement).
- Purchasing Group: The buyer or the group responsible for negotiating and processing the purchase order.
Pricing Information
- Price: The price of the material as agreed with the vendor. This can include various conditions such as the base price, discounts, and surcharges.
- Currency: The currency in which the transaction will take place.
- Valid Dates: The period during which the price and conditions are valid.
- Price History: A log of prices that have been used over time for the material from this vendor.
Delivery Information
- Delivery Times: The time it takes for the supplier to deliver the material after an order is placed.
- Shipping Conditions: These define how the material will be transported from the vendor to the buyer.
- Delivery Tolerances: Tolerances in terms of quantity or date beyond which deliveries will be considered late or incomplete.
Conditions and Agreements
- Discounts and Surcharges: Conditions applied to the material price, which may include discounts for bulk purchases or extra charges for special handling.
- Incoterms: International commercial terms that specify the responsibilities of the buyer and the seller regarding shipping and delivery (e.g., FOB, CIF).
- Minimum Order Quantities: The minimum quantity of material that must be purchased from the vendor to receive a particular price or terms.
Vendor Specific Data
- Order Unit: The unit of measure in which the material will be ordered from the vendor (e.g., pieces, kilograms, etc.).
- Standard Order Quantity: The standard quantity that is typically ordered for this material.
- Material Status: Specifies if the material is active, blocked, or under some special conditions (e.g., under review for quality issues).
Quality and Inspection Information
- Quality Control: Information regarding the quality inspection of materials delivered by the vendor. This may include criteria for accepting or rejecting the goods based on quality standards.
- Batch Management: In some cases, batch management data can also be included in the PIR, allowing the system to track materials by batch numbers.
Price Determination
- Price Control: The method by which the price is determined for the material in the system (e.g., fixed price, price based on purchase order).
- Access Sequences: These define the order of conditions or rules used to determine the price from various sources, such as the info record, price list, or contract.
Why is the Purchasing Info Record Important?
- Efficient Procurement Process: The PIR reduces the need to input the same information repeatedly by storing vendor-material-specific data. It speeds up the creation of purchase orders (POs).
- Price Transparency: It helps in managing and reviewing the pricing and conditions agreed upon with vendors, providing transparency on costs, discounts, and delivery conditions.
- Improved Vendor Relationship: By maintaining specific information about the vendor and material in one place, organizations can better track supplier performance, manage contracts, and ensure that all terms are met.
- Reporting and Analysis: The data within the PIR can be used for reporting purposes, such as analyzing the procurement process, price trends, and vendor performance.
Types of Purchasing Info Records
- Standard Info Record: Used for standard purchases where there is no long-term agreement (e.g., no purchase contract) between the vendor and the buyer.
- Contract Info Record: Created when a contract is in place with a vendor. It stores details like contract validity and pricing for materials over a specified period.
- Quotation Info Record: If a quotation is received from a vendor, this info record can be created based on the quotation details. It includes pricing and conditions tied to that specific quote.
Creating and Maintaining PIR in SAP
- Transaction Code: The transaction code to create or maintain a purchasing info record is ME11 (for creation) and ME12 (for modification).
- Information Flow: Typically, PIR is created manually when a new vendor-material relationship is established or automatically generated when a purchase order or contract is created, depending on the system setup.
Example
Suppose a company buys a specific type of raw material from a particular supplier. The Purchasing Info Record would include the following information:
- Supplier’s name and ID.
- Material number and description.
- The agreed price for the material.
- Delivery timeframes.
- Terms of delivery (Incoterms).
- Minimum order quantities and order units.
When the purchasing department wants to order that material again, they can refer to the PIR, which helps in quickly generating a purchase order with the correct terms. Conclusion:
Summary
In summary, the Purchasing Info Record (PIR) is crucial for efficient and streamlined procurement processes in SAP. It not only consolidates all relevant details about a vendor and material but also enables better vendor management, pricing accuracy, and smoother purchasing operations.
Customizing
Conditions from reference purchasing organization to purchasing organization
It is possible to inherit conditions that are maintained in an info record at EkOrg and/or plant level for a reference purchasing organization, e.g. in purchase orders with any purchasing organization.
The prerequisite here is that the EkOrg X is assigned to the reference EkOrg Z in Customizing. In addition, the document field for EKORG must be adjusted to EKORG1 in the access sequence, e.g. for the material info record (plant-specific).
The best way to do this is to copy the existing material plant info record:
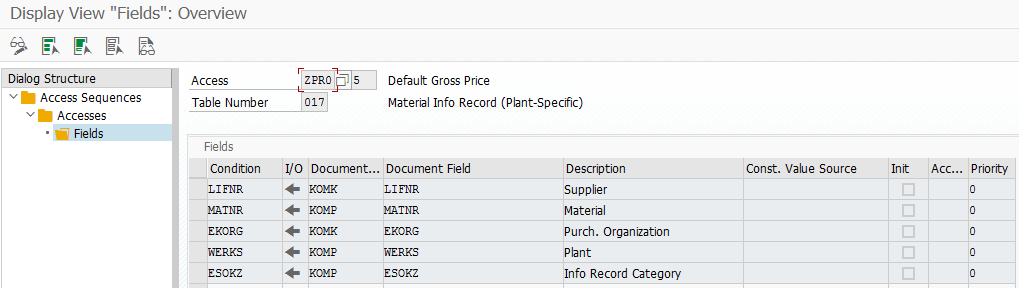
to
